The Rise of North American Graphite in Green EV Technologies
China Has a Monopoly
Over the past 20 years, China has invested heavily in its domestic battery and critical minerals industries. For example, China now accounts for 96% of the world’s supply of battery grade graphite anodes. The net effect of this near-monopoly is that EV battery producers all over the world are dependent on Chinese suppliers for their critical minerals.
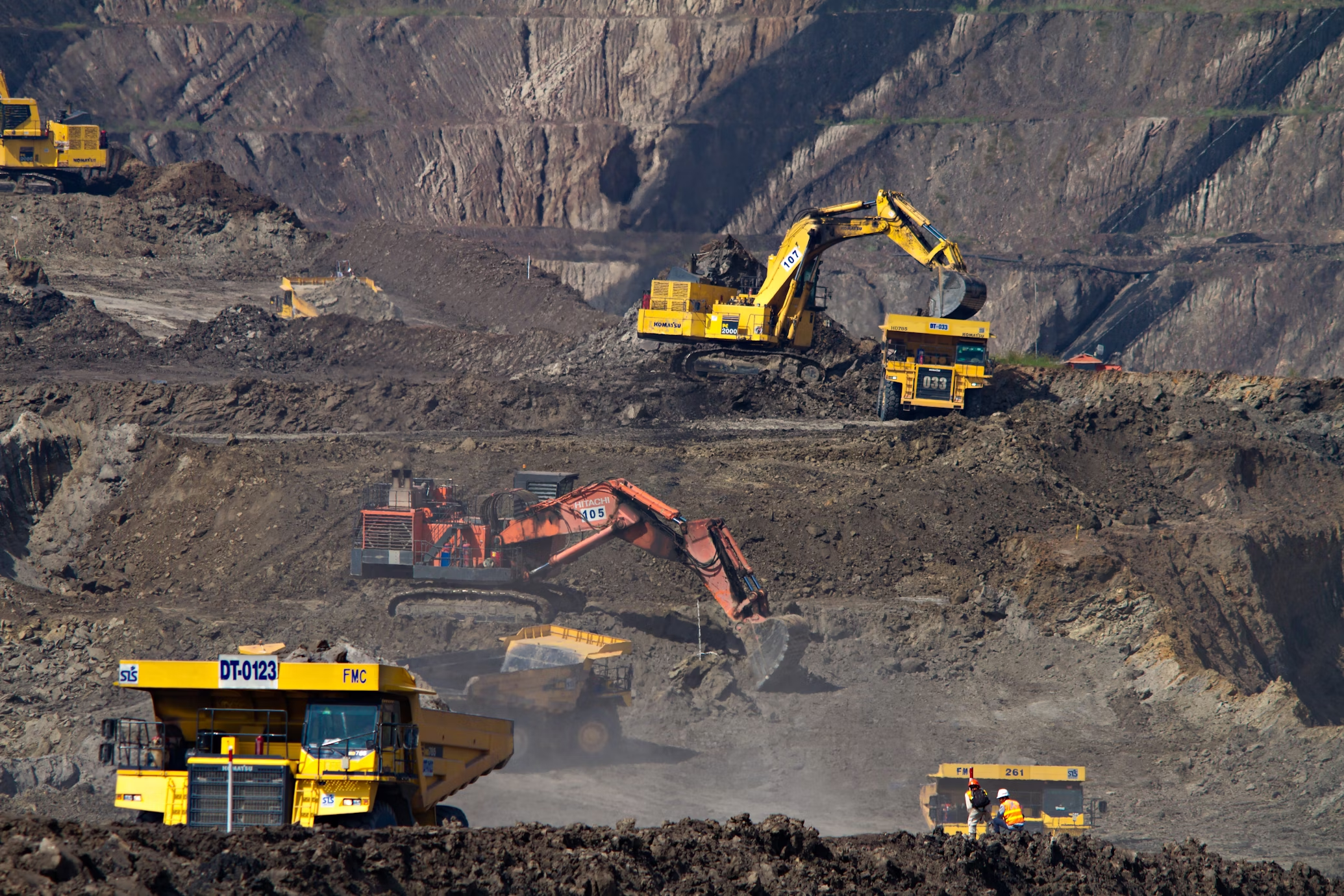
Incentivizing North American Graphite Use
Battery manufacturers have a strong commercial incentive to purchase North American source graphite. Tax credits from the Inflation Reduction Act add up to $35/kWh for cells and $10/kWh for packs produced in North America. However, to receive these incentives under the IRA, a minimum of 50% of battery materials must be produced or recycled in North America. Less than 1% can be produced in China. Battery producers’ supply chains were further complicated by the US Treasury which issued “Foreign Entity of Concern” (FEOC) regulations. These capped Chinese ownership of IRA compliant producers at 25%. This legislation underscores the strategic importance of developing domestic sources for these critical materials. This in turn reduces the dependence on foreign supplies and enhances the sustainability of the domestic EV battery industry.
The Green Advantage of Recycling Graphite Anodes
Recycling graphite not only conserves resources but significantly lowers environmental impacts from traditional graphite production. The advantage of using recycling to produce new battery graphite is that the starting material is already battery-grade graphite. Thus, the very large amount of energy and greenhouse gas emissions associated with the production of virgin graphite are not required.
Optimal Time for North American Graphite Innovation
Several factors coalesce to make this an ideal time to commercialize graphite recycling technology. The US government has a goal of making 50 percent of all new vehicle sales electric by 2030 (The White House 2021). Under the Inflation Reduction Act, advanced manufacturing credits give the producer a payout from the Treasury (Solar Energy Technologies Office 2023). The production of battery cells qualifies for a credit of $35 per kilowatt-hour of capacity, and the production of battery modules qualifies for $10 per kilowatt-hour. Companies can also be reimbursed 10% of the costs incurred due to the domestic production of electrode active materials, like the cathode and anode. This includes the graphite anode under the Advanced Manufacturing Production Credit.
These financial incentives are designed to spur investment in the EV sector, particularly in the production and recycling of critical materials. They reflect a broader strategy to secure the United States’ position as a leader in the global transition to electric transportation.
The Growing Demand for Battery Factories
As a result of these incentives, the number of battery factories either planned, under construction or operational in the country has increased 15-fold between 2019 and 2023 (Bellan 2023). The resulting annual manufacturing capacity will increase to over 1,200 gigawatt-hours before 2030. This is enough batteries for 18 million EVs if each factory reaches maximum capacity. A map of these proposed factories illustrates the rapid growth of the industry and the strategic importance of supporting its supply chain through innovations in recycling and material sourcing.
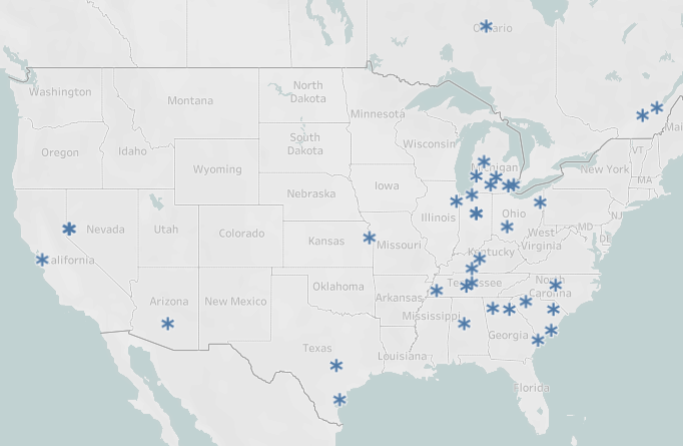
Benchmarking the Future Demand
After 2027, investments in additional synthetic graphite production capacity will need to increase to meet demand in the battery sector (Rystad Energy 2022). By 2030, the supply gap in Chinese flake graphite is expected to be ~1Mt, increasing to over 5Mt in 2040 (Benchmark Minerals Intelligence 2023), due to an increased penetration rate of EVs (43% in 2030, 76% in 2040). EV adoption may prove to be even faster than projected – in certain countries such as Norway, battery electric vehicles (BEVs) already account for 88% of new vehicle sales.
Sustainable North American Graphite Production via Direct Recycling
Adopting direct recycling methods marks a critical step towards achieving environmental sustainability and addressing material scarcity through:
- Developing Alternatives to Scarce Critical Materials: Direct recycling reduces the need for new production of scarce battery-grade graphite and other cathode materials in the United States.
- Promoting Efficient Production, Use, and Recycling: This approach enhances the US graphite supply chain, ensuring the sustainable use of critical minerals.
- Securing a Long-term, Sustainable Supply: Direct recycling practices guarantee a sustainable supply chain for graphite and essential materials over the long term.
- Prioritizing Work in Underexplored Areas: The direct recycling sector, still in its infancy, presents opportunities for innovation and addressing financial and technical challenges.
- Revolutionizing Production: Characterized by low cost, minimal energy requirements, and high efficiency, direct recycling methods are disruptive technologies in the recycling industry.
- Optimizing Cost, Environmental Emissions, and Resource Usage: Compared to traditional methods, these recycling processes are less resource-intensive and produce materials with enhanced properties, such as through pre-lithiation.
- Diversifying Sources and Reducing Environmental Impact: Utilizing green chemistry and fully recyclable solvents, direct recycling lowers operating costs and environmental impacts, contrasting with methods like pyrometallurgy or hydrometallurgy that are more resource-intensive and generate significant waste.
The integration of environmental sustainability with technological innovation in direct recycling methods provides a promising outlook. As EV adoption grows, prioritizing recycling and sustainable material sourcing is crucial. The current initiatives and incentives are key to guiding the industry toward a more sustainable and eco-friendly direction.
James White PhD and Joseph Moniodis PhD | 11th April 2024
Citation: James White and Joseph Moniodis. 2024. “The Rise Of North American Graphite In Green EV Technologies.” Carbon Critical. https://carbon-critical.com/north-american-graphite-in-green-ev-technologies/.
References
Bellan, Rebecca. 2023. “Tracking the EV battery factory construction boom across North America.” Tech Crunch, 2023. https://techcrunch.com/2023/08/16/tracking-the-ev-battery-factory-construction-boom-across-north-america/?guccounter=1&guce_referrer=aHR0cHM6Ly93d3cuZ29vZ2xlLmNvbS8&guce_referrer_sig=AQAAAFjvwApvJZFr-c_kPp7QdnofMNYL7k7QD0E9jYDLa-KOTRuG5aGrtlmGke9V-TdYqP-OI.
Benchmark Minerals Intelligence. 2023. “Flake Graphite Forecast.” 2023.
Greenpeace Asia. 2017. “Greenpeace report troubleshoots China’s electric vehicles boom, highlights critical supply risks for lithium-ion batteries.” YouTube: Home. https://www.greenpeace.org/eastasia/press/6175/greenpeace-report-troubleshoots-chinas-electric-vehicles-boom-highlights-critical-supply-risks-for-lithium-ion-batteries/.
Rystad Energy. 2022. “Fake it till you make it: Synthetic graphite holds the key to meeting battery demand surge, despite ESG concerns.” Rystad Energy. https://www.rystadenergy.com/news/fake-it-till-you-make-it-synthetic-graphite-holds-the-key-to-meeting-battery-dema.
Solar Energy Technologies Office. 2023. “Federal Tax Credits for Solar Manufacturers.” Department of Energy. https://www.energy.gov/eere/solar/federal-tax-credits-solar-manufacturers.
The White House. 2021. “FACT SHEET: President Biden Announces Steps to Drive American Leadership Forward on Clean Cars and Trucks.” The White House. https://www.whitehouse.gov/briefing-room/statements-releases/2021/08/05/fact-sheet-president-biden-announces-steps-to-drive-american-leadership-forward-on-clean-cars-and-trucks/.